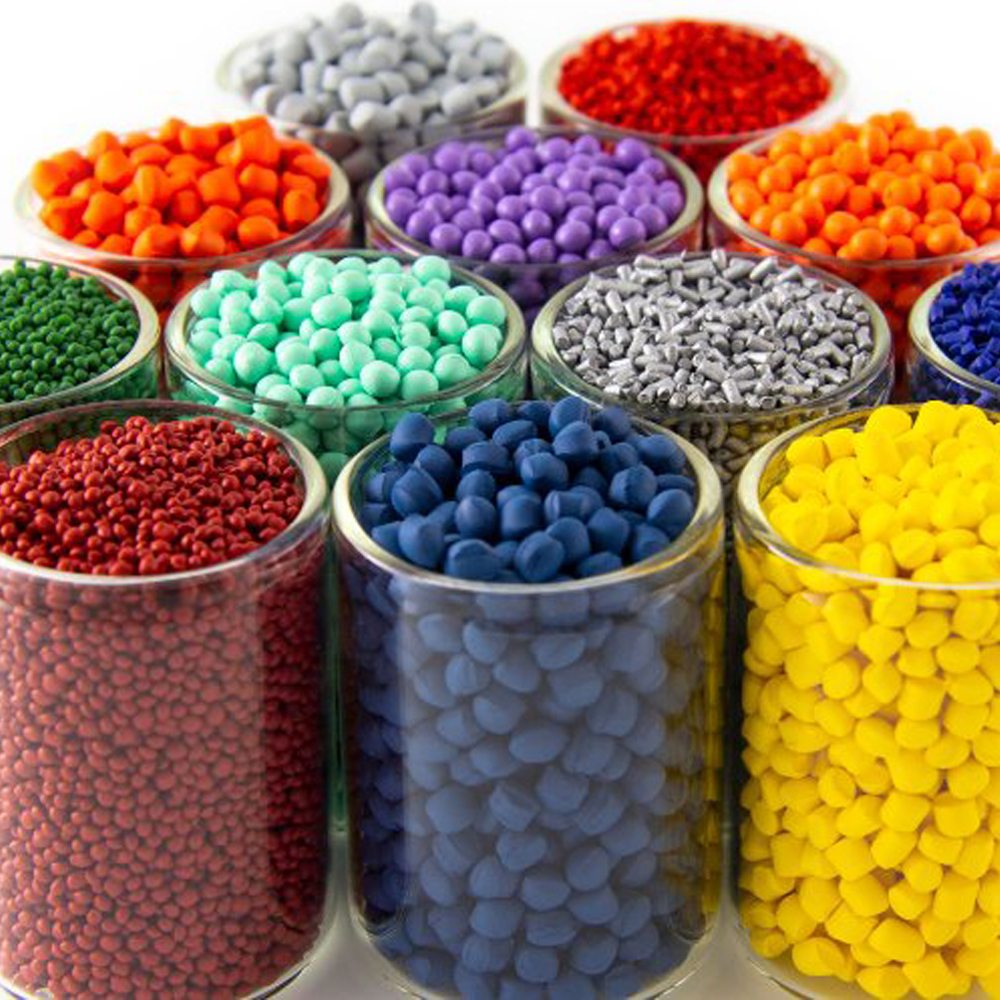
What is Masterbatch and Its Advantages?
In brief, masterbatch serves as a solid plastic additive utilized for coloring plastics or enhancing their properties.
A masterbatch is a concentrated blend produced by combining colorants and additives into a polymer carrier through heat treatment, often employing a high shear mixing extruder. Afterward, the mixture is cooled, sliced, and shaped into granules using a pelletizer.
Masterbatch offers a cost-effective means for coloring raw polymer during the plastics manufacturing process.
A color masterbatch, also known as a color concentrate, is a granular material employed for coloring thermoplastics. It comprises one or more colorants and a carrier resin specifically tailored to the polymer. The combination of components in a color masterbatch is referred to as its formulation.
Masterbatches possess a high concentration with substantial “let down ratios,” where one ton of natural polymer can be accommodated in a 25 kg bag.
Masterbatches enable the dilution of natural materials, allowing for precise dosing of costly components.
The solid crystals in masterbatches are devoid of solvents and typically exhibit an extended shelf life since the polymer’s solvent does not evaporate. They generally contain 40-65% additives, though this range can vary from 15-80% in certain instances.
In contrast to using raw pigments, masterbatch offers a superior level of precision in regulating the opacity or transparency of finished colored items.
Masterbatch incorporates pre-established proportions of additive components, thus minimizing the likelihood of deviations throughout the production process.
When dealing with substantial production volumes, masterbatching delivers enhanced color uniformity to users.
The fusion processes are optimized as masterbatch’s binding agents are tailored to the specific polymers in use.
In contrast to masterbatch, pigments can become airborne during processing, potentially causing cross-contamination in neighboring manufacturing lines.
Simplified Addition of Additives:
Masterbatches offer a more straightforward method for incorporating additives, whether it’s through pellet-to-pellet mixing or direct extruder addition. The need for specialized dosing equipment for minimal dust quantities is eliminated, and it enhances the precision of adding the same rate of additive in the final product.
Enhanced Product Uniformity and Process Reliability:
Utilizing an additive masterbatch also elevates product consistency and process stability by achieving better dispersion.
Safer Handling of Hazardous Substances:
Numerous additives are inherently hazardous or prone to degradation in their pure form. Masterbatches encapsulate these additives within a polymer resin or liquid, reducing or, in many cases, entirely eliminating their potential dangers. This approach also eliminates the multiple risks associated with handling powdered substances. Consequently, it leads to reduced technical controls and decreased personal protective equipment (PPE) requirements.
Cleaner Manufacturing:
Besides being safer to handle, masterbatch additives also contribute to a cleaner production environment. There are no airborne color pigments or other powdered additives that can scatter, spill, or statically adhere to surfaces. This results in a cleaner production area, minimized cross-contamination, and potentially swifter transitions between different product runs.
Enhanced Additive Stability and Extended Shelf-Life:
Masterbatch solutions can safeguard additives from exposure to humidity, temperature fluctuations, and UV radiation during storage.
Streamlined Integration of Antimicrobial Technology:
Research demonstrates that incorporating antimicrobial technology is made as straightforward as possible for our customers, capitalizing on the extensive benefits offered by concentrated masterbatch formulations.
Learn more knowledge and trends in masterbatch industry from our blog.
In brief, masterbatch serves as a solid plastic additive utilized for coloring plastics or enhancing their properties.
Discover the world of masterbatch additives in this comprehensive guide to the seven most common types of masterbatch used in the polymer industry.
The production of masterbatch involves a range of techniques and processes, each carefully executed to ensure the highest quality end product. This manufacturing journey can be broken down into the following crucial stages.
©2023. All Rights Reserved.
Our team will send back the best offer in 20 minutes.