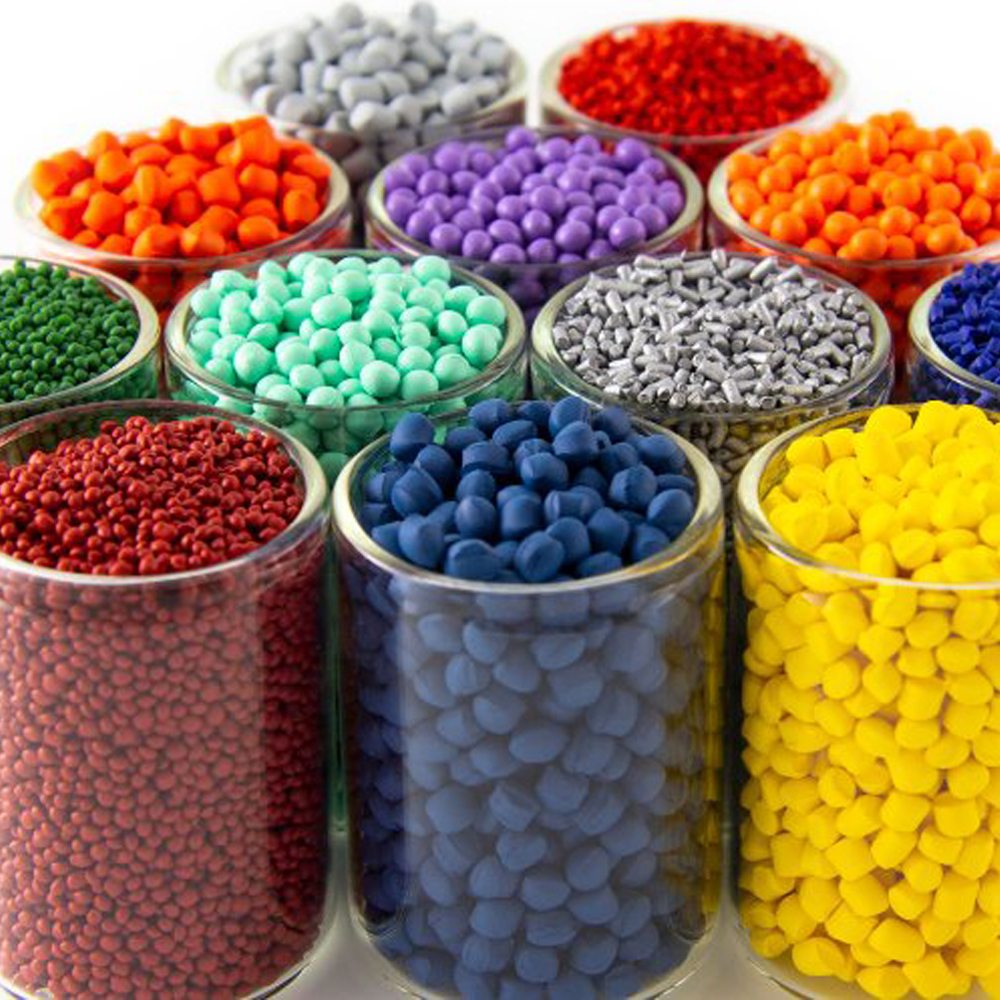
What is Masterbatch and Its Advantages?
In brief, masterbatch serves as a solid plastic additive utilized for coloring plastics or enhancing their properties.
The initial step in masterbatch production involves the precise measurement and weighing of materials such as toner, carrier, and additives. Accuracy in this phase is paramount to achieving the desired properties in the final product.
Once the materials are accurately weighed, they are introduced into a mixer where they undergo thorough mixing. This blending process ensures a homogeneous distribution of pigments and additives throughout the mixture.
The mixed materials then pass through a controlled heat process, known as extrusion, where they are fused into a carrier material. This stage is crucial for achieving the desired properties and characteristics of the masterbatch.
Following the extrusion process, the concentrated mixture is allowed to cool and dry. This cooling and drying phase results in the transformation of the mixture into various forms, including powders or granules, depending on the intended application.
The final masterbatch product is meticulously packaged according to the specific requirements of customers, ensuring convenience and ease of use in downstream processes.
Successful masterbatch manufacturing requires careful consideration of several essential factors to ensure product quality, consistency, and environmental responsibility.
Maintaining a high standard of quality begins with the selection of premium-grade materials, including pigments and additives. The entire manufacturing process must adhere to rigorous quality control measures to ensure that the final product meets industry standards.
Sustainability and eco-friendliness are critical considerations in the masterbatch manufacturing process. Selecting environmentally friendly materials and adopting sustainable practices are imperative for producing eco-conscious products that have a minimal impact on the environment.
To achieve consistency and reliability, materials must undergo an accurate manufacturing process. This includes maintaining the correct proportions of materials and ensuring uniformity throughout the production process. Quality control measures should be in place to guarantee that all requirements are met.
For color masterbatch production, achieving precise color accuracy is essential. The correct pigment proportions are critical in attaining the desired color, and the resulting color should remain stable under various conditions, enhancing the visual appeal of the final product.
Masterbatch materials must be compatible not only with each other but also with the specific manufacturing process in use. Material compatibility plays a significant role in ensuring the success of the masterbatch and the quality of the final product.
Efficiency in production is key to maintaining cost-effectiveness without compromising product quality. Reducing raw material wastage and maximizing production efficiency are strategies that contribute to cost-efficient manufacturing.
Strict adherence to regulatory norms throughout production, packaging, and transportation is crucial for safety and security. Compliance with established regulations ensures that the product meets all necessary safety and quality standards.
Throughout the masterbatch manufacturing process, it is vital to prioritize customer requirements. This includes addressing every aspect, from pigment selection to product transportation. Consideration of how the manufacturing process affects the product’s properties, as well as factors like packaging, labeling, and transportation, is essential in delivering a product that meets and exceeds customer expectations.
Masterbatch manufacturing is a meticulously orchestrated process that encompasses various stages, each critical in producing high-quality and versatile products. From precise material weighing and thorough pigment mixing to extrusion, cooling, and tailored packaging, every step contributes to the creation of masterbatches that meet the diverse needs of industries and applications.
In the pursuit of excellence in masterbatch manufacturing, it is imperative to consider multiple factors. Quality takes center stage, demanding the selection of top-tier materials and adherence to strict quality control standards. Environmental responsibility underscores the importance of sustainable practices and eco-friendly materials, ensuring that our products have a minimal environmental footprint.
Precision in manufacturing, color accuracy, compatibility, and cost-efficiency are essential components of a successful manufacturing process. Attention to detail in meeting regulatory compliance requirements ensures both safety and product quality. Finally, a customer-centric approach is paramount, addressing not only the technical aspects of production but also the delivery and support services that enhance the overall customer experience.
By embracing these principles, masterbatch manufacturers can not only produce exceptional products but also contribute to a more sustainable and environmentally conscious industry. The journey of masterbatch manufacturing is a complex and multifaceted one, but it is through dedication to excellence and continuous improvement that we pave the way for innovation and progress in the world of plastics.
Learn more knowledge and trends in masterbatch industry from our blog.
In brief, masterbatch serves as a solid plastic additive utilized for coloring plastics or enhancing their properties.
The production of masterbatch involves a range of techniques and processes, each carefully executed to ensure the highest quality end product. This manufacturing journey can be broken down into the following crucial stages.
Discover the world of masterbatch additives in this comprehensive guide to the seven most common types of masterbatch used in the polymer industry.
©2023. All Rights Reserved.
Our team will send back the best offer in 20 minutes.